You have a brilliant idea. It could transform how your team operates and boost efficiency. However, everyone is too busy to even think about improvement. This scenario is all too common in many organizations: as a leader, you are swamped, your team is overwhelmed, and innovation seems out of reach. Implementing lean seems impossible.
What You Should Know About Lean?
One thing to remember: Lean is not an or overnight solution.
Pioneered by Toyota, Lean principles have revolutionized industries around the world. In today’s fast-paced business environment, Lean stands out for its simplicity and effectiveness. It’s a powerful approach designed to boost efficiency, reduce waste, and drive innovation.
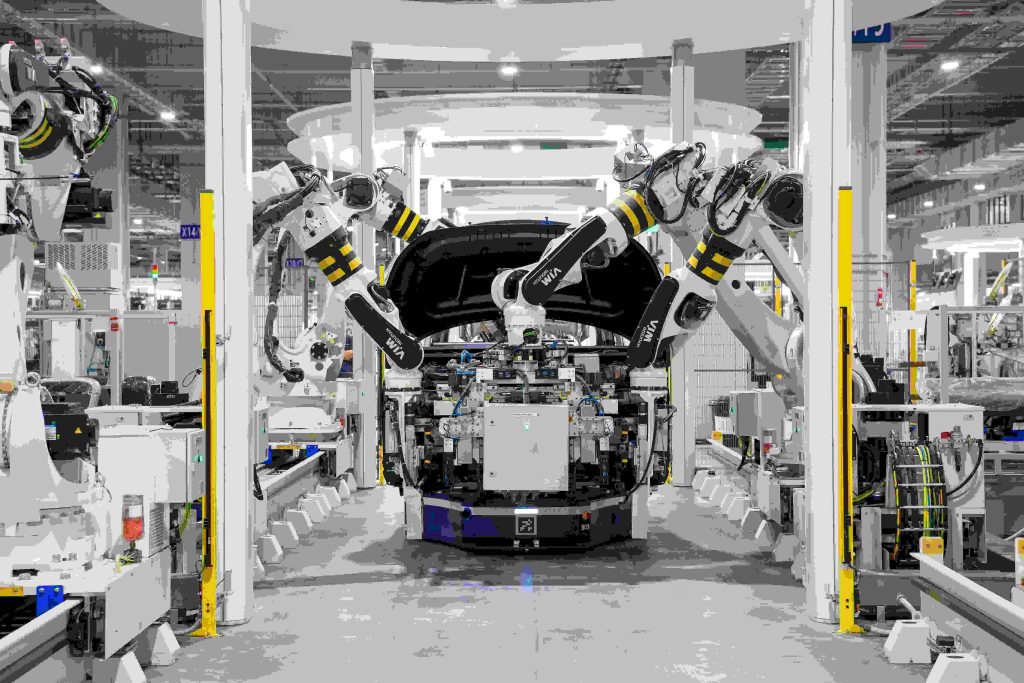
Problem Solving
Lean’s backbone is continuous improvement and practical problem-solving. The PDCA (Plan-Do-Check-Act) cycle provides a simple, step-by-step guide to identifying and solving issues. The 5 Whys technique, another handy tool, digs deep by asking “why” multiple times to uncover the root cause of problems.
Just-In-Time (JIT)
JIT is all about producing just what’s needed, when it’s needed, and in the right amount. This minimizes waste and keeps inventory costs low. In lean principle, it involves calculating Takt time to match production pace with customer demand, Kanban for signal of production needs and work-in-progress, etc.
Kaizen
Kaizen means “continuous improvement” and encourages everyone, from the CEOs to the working floor employees, to look for ways to improve. Small, everyday changes can lead to big improvements in efficiency, quality, and morale.
Lean as the Accelerator of Industry 4.0
Lean is a game-changer for businesses aiming to thrive today. Combining Lean practice with Industry 4.0 technologies like IoT, big data, and AI takes efficiency to the next level. While the technologies enable smart automation and data-driven operation, lean is making operations even smoother and more productive. The progress is slow, the changes are tiny. But It is a recipe for sustainable success, staying agile, driving growth and staying ahead in the competitive landscape.
CONCLUSION: GOOD LEADERS LEAD TO LEAN
Knowing lean and knowing how to encourage lean at your organization are two different stories. Small changes come from everyone, and a good leader should knows how to get everyone involved. It is about creating a culture where everyone is empowered to make things better. And there you have it – Lean isn’t just about streamlining processes; it is also a perfect example of effective leadership in action.
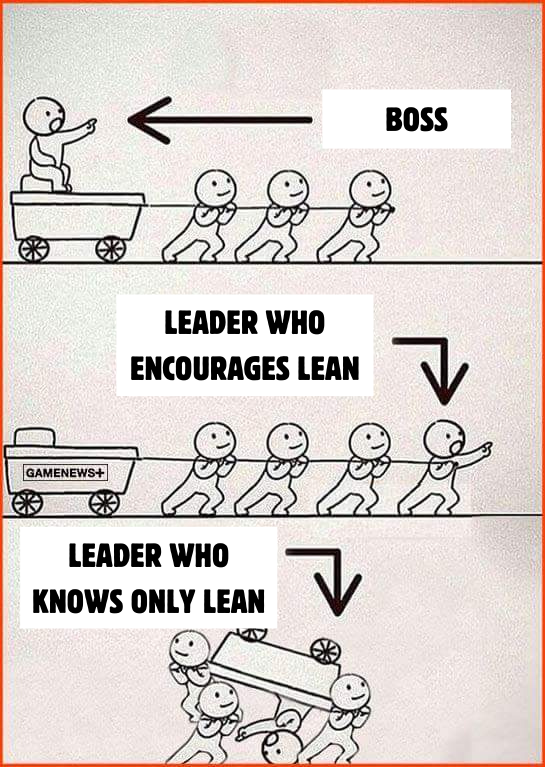
Article written by Marilyn Wong, Conference Producer (APAC) at Zenith Bizness Excellence, Kuala Lumpur.